切板とは
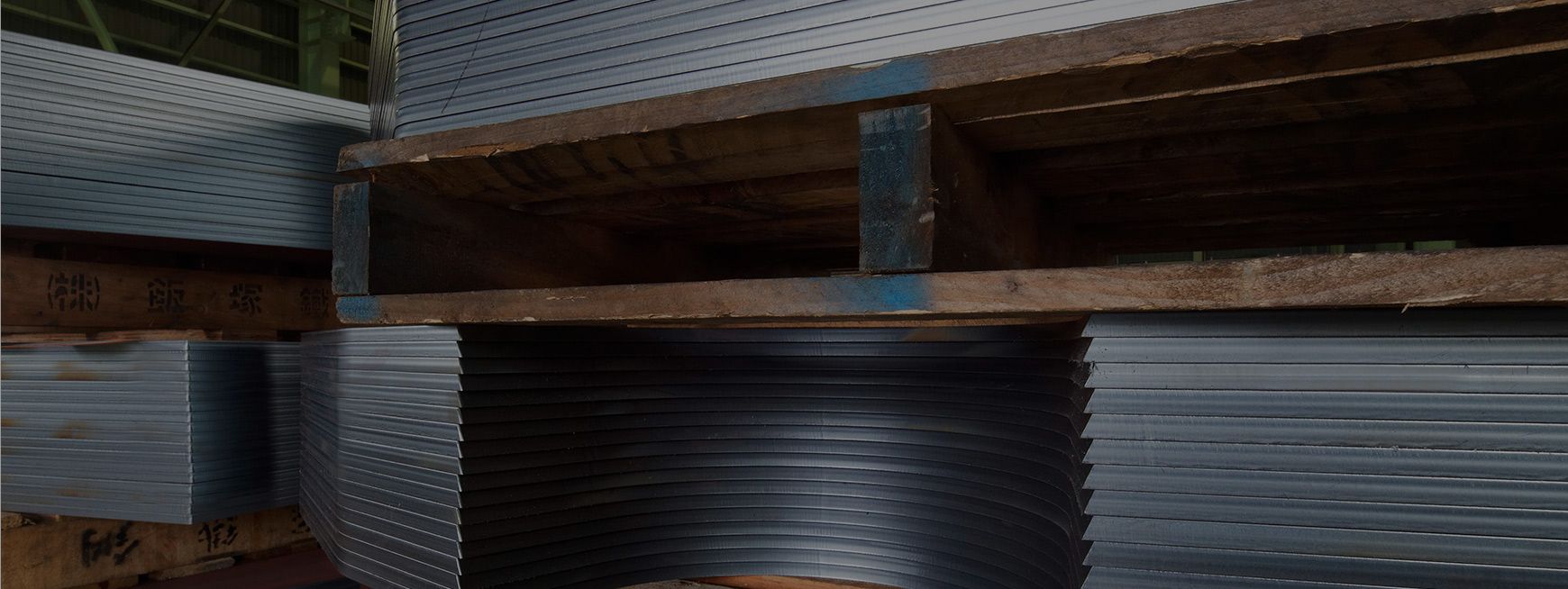
切板の定義
切板とは?
厚中板を需要家の希望する指定寸法に、ガス溶断機等により切断加工するもの。
(一般的に、シャーリングマシンで切断することをシャー切断、ガス等熱源で切断することを溶断と呼ぶが、この加工業を総称して“熔断業”と呼ぶ。)
熔断業の役割
鋼材需要流通機構の中間にあって、製鉄メーカーに対しては販売網の一役として、
また、需要家へは切断加工の有利性(歩留り、工賃、品質上)と即納在庫により経済流通のニーズに貢献している。
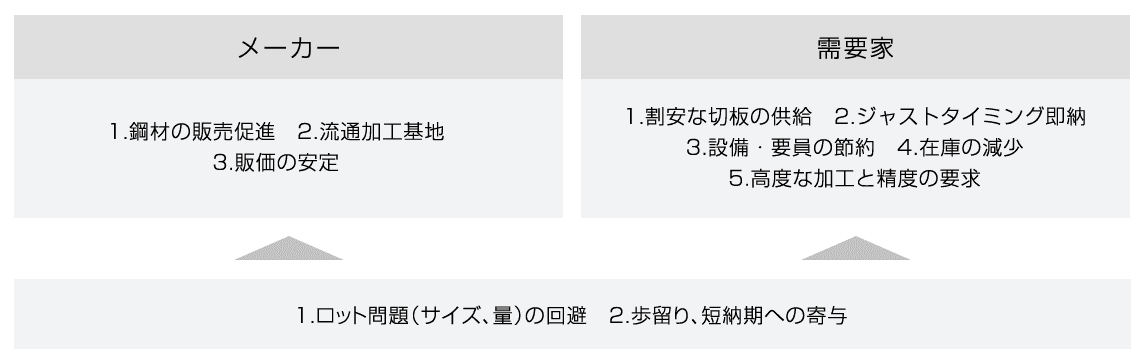
シヤリングは特定の切断方法を意味するが、一般的に、熔断業=シヤリング業と理解されている。
熔断業者の位置付
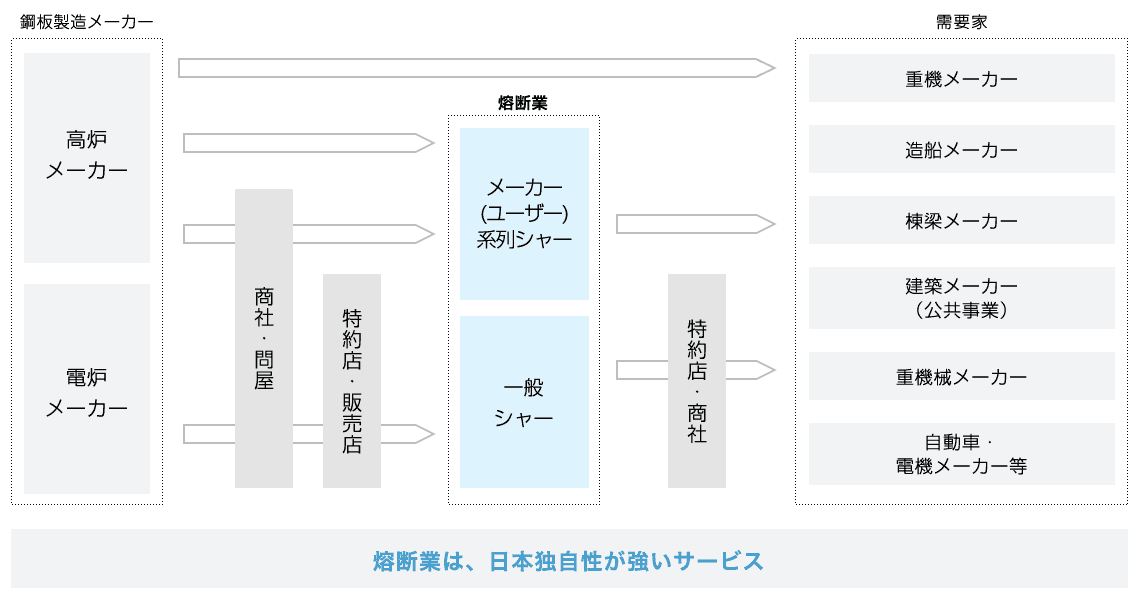
切板の歴史
創始時代(1909年~1919年)

1909年(明治42)大阪において古川庸男氏が英国製のシャーリングマシンを輸入し、
我が国最初の民間熔断工場を設立し、熔断業を創始した。
重工業化への寄与(1920年~1930年)
また、材料(鋼板)は商社を通じ製鉄メーカーから発生品を購入した。昭和初期には、厚板鋼板を購入するようになった。
製鉄メーカーと熔断業との連携(1950年~1959年)
製鉄メーカーから一級鋼板の供給が再開された。
熔断技術の進歩(1954年~1965年)
ガス溶断においては、小型の溶断機からフレームプレーナー※1が導入され、鋼板の溶断を精密かつ量的に行えるようになった。
1965年代からはアイトレーサー※2付きならい溶断機が普及し、機械、構造物の異形型溶断加工が出来るようになり、需要家によろこばれた。
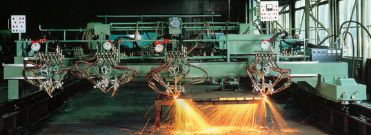
※1.フレームプレーナー
自動ガス切断機*の一種で,電動台車に多数のトーチを取り付けて,多数の平行な切断を同時にできるようにしたもの
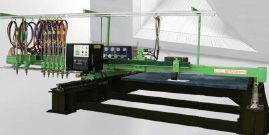
※2.アイトレーサー
光電管による図形読取り装置とトーチの走行装置を連動させ,複雑な形状の部材*を容易に切断することのできる一種の自動ガス切断機
需要家と溶断業との連携
参考文献;全国厚板シヤリング工業組合 (鉄鋼の初歩知識とシヤリング業のあらまし)
切板の切断方法
鋼板のメジャーな切断方法
機種 | 切断方法 | メリット | デメリット |
---|---|---|---|
ガス切断 | 燃料と酸素の混合ガスの高熱炎により切断する方法。 | 一般的に普及している切断方法。幅広い板厚に対応。安価で加工出来る。 | 熱影響を受けて歪が発生することがある。 |
プラズマ切断 | プラズマアークとガスにより、溶融部を吹き飛ばして切断する方法。 | ガス切断よりも極めて切断速度が速い。単品切に向いている。 | 消耗品等、高コスト。また、小さな穴開けには向いていない。 |
レーザー切断 | レーザー発振器を用い、レーザービームをレンズで集光して鋼板に照射切断する方法。 | もっとも切断精度が期待できる切断方法。高コストながら無人運転も可能で生産性が期待出来る。 | 初期投資及び、ランニングコストが高い。 |
シャー切断 | シャーリングマシン等で機械的にせん断する方法。 | ランニングコストが安く、加工費が抑えられる。 | 切断部減厚の可能性有り。異形切断は出来ない。 |
ガス切断
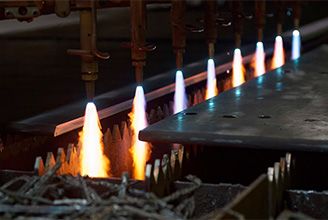
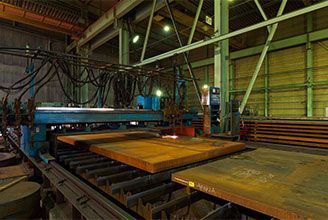
燃料(アセチレン・プロパン・水素等)と酸素の混合ガスを用いて、高熱炎により溶断するもので、切断範囲は一般的に鋼板厚 6m/m 程度から極厚の200m/m 超え程度の広い範囲での切断が可能。
特徴
異型物から極厚まで切断が可能。多大な熱量をかけ切断部位を溶融させる切断方法の為、切断鋼板に熱影響を与えやすい欠点を有するが、切断コスト面では比較的安価である。切断精度は条件にもよるが±1.0mm の範囲内に収まるのが一般的である。
切断面
適正な切断条件(切断速度・ガス圧等・火口の選択等)をもとにして、平滑な切断面を得ることができる。切断面における欠陥として、粗さ・ノッチ・エグレ・切断面の倒れ・上縁の溶けなどが発生することがある。 これらの不良発生を防ぐ為、切断鋼板の板厚に見合った切断条件を確保することはもとより、振動のない安定した環境と火口等の器具類の整備を行なう必要がある。 また、細長い製品は熱影響による歪も懸念される。
プラズマ切断
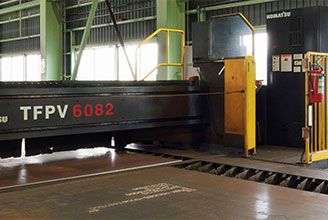
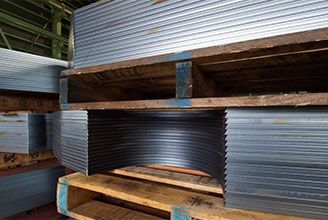
プラズマアークに動作ガス(酸素・窒素・エアー等)と拘束ノズルで熱的ピンチ効果を与え、高温で鋼板切断部を溶融させプラズマ気流で吹き飛ばし切断するもので、一般的に切断範囲は6m/m から40m/m程度である。
特徴
ガス切断等に比べ極めて切断速度が高速であり、切断鋼板に対するトータル加熱量も少なく熱影響が軽減される。切断精度は条件によるが±1.0mm の範囲内に収まるのが一般的。切断時に、有害な煙ヒュームが発生するため強力な集塵設備を併設せねばならない場合がある。
切断面
プラズマアークの特徴として通常切断面の倒れが発生する。この倒れを補正するために、板厚や切断状況に合わせトーチの角度を可変にする機構が必要となる。切断面自体は、滑らかであるが若干の丸みを呈し厚みが増大するほど顕著になる傾向がある。また、高速切断と溶融幅が大きいことから、製品角はR形状になることがある。
レーザー切断
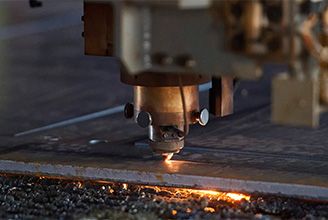
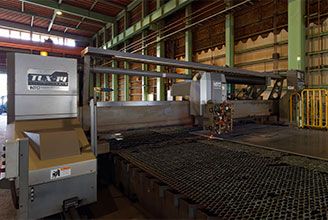
レーザ発振器(切断用熱源として炭酸ガスを用いるのが一般的)内部で発生させたレーザビームを集光し、直接鋼板の切断部位に照射して局部的に溶融させ、アシストガスにより溶融部分を吹き飛ばし切断する方法で、切断範囲は一般的に現在、薄物から板厚22m/m 程度の範囲で切断が可能。
特徴
加熱部位が局所的の為、切断鋼板に対する熱影響はほとんど無く微細な切断が可能である。火力を用いない為、長時間の無監視運転が可能である。切断精度は、これも条件によるが初期設備投資にも、その後の切断コストも決して安価ではないが、それを補ってでも余りある生産性が期待できる。
切断面
切断面粗度は、決して他の切断法に比して高い水準ではないが、粗さの間隔・深さが微細の為好印象を与える。 また、ガスやプラズマでは加工の出来ない小さな抜き穴加工が出来る為後の機械加工を免除出来ることもある。
シャー切断
シャーリングマシン等により機械的にせん断する切断方法で、切断可能範囲は薄板から厚板の12m/m 迄位が一般的であるが、 大出力機となると25mm位までが処理可能なものもある。
特徴
通常は無加熱切断の為、鋼板に対し歪等の熱影響を与えることがない。
切断面
機械的圧力でせん断する為、切断面周辺の減厚がある。切断面における欠陥として、ダレ、カエリ、段差、二次せん断等が発生することがある。 また、細長い製品はネジレが発生する。